Let the application dictate the machine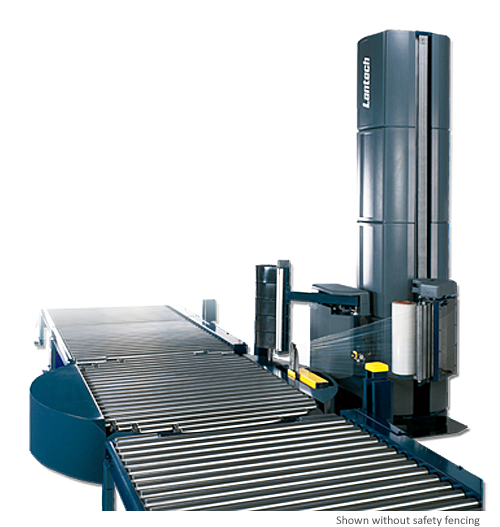
In a recent article Decoding the Terminology of Stretch Wrappers, we explored the difference between automatic and semi-automatic wrapping. Our industry’s traditional terminology tends to reinforce the perception of a stark differentiation between two very different solutions – and that can discourage some creative approaches to application requirements.
One example is the various applications for a stand-alone automatic. When discussing an automatic pallet wrapper we often picture an integrated, in-line system with pallets flowing continuously from the production line and palletizer, straight through the pallet wrapper and off to the warehouse. Certainly those applications exist. But there are many applications for automatic wrappers that stand alone.
Safety and fork truck “no go zones”
Stand-alone automatic stretch wrappers are sometimes located in production and operational sections of a factory which are not major material handling areas.
Potentially tight spaces, combined with the presence of workers and equipment in those areas, often mean that fork truck access is limited – or that operations, safety and engineering would love to restrict fork truck traffic if possible.
While pallet jack operations demand training, safety measures and awareness, they are generally better suited to those sorts of areas than fork trucks. And we find it’s not unusual for companies to create no-go zones for fork lifts.
A resulting complication is how to load automatic stretch wrappers using conveyors with pallet jacks. Often they’re unloaded with fork trucks but sometimes unloading with pallet jacks is also required.
So what’s the work around? It’s a scissors lift. This is a special conveyor whose top is flush with the floor. The pallet jack operator places the load on the conveyor, backs away, activates the conveyor, which then rises to the system’s pass height and transports the load to the next conveyor or to the turnbale. When the transfer is completed, the scissors lift conveyor lowers so it’s flush with the ground and ready for the next load. The same idea can be applied to the exit side of the wrapper if necessary.
The drawbacks to scissors lifts are that they’re expensive and a pit must be created in the floor to accommodate the scissors mechanism and motor.
But yes, a pallet jack can be used with an automatic stretch wrapper. Click here to see the specification sheet.
The larger context
If you’re wrestling with some challenging stretch wrapping criteria, take a look at our Automatic Stretch Wrapper Buying Guide. It’s loaded with lots of helpful tips to find the right machine today, but more importantly offers insights into what’s new that might change the way you think of your stretch wrapping application.
You’ll find the free download here.
This post was published on November 17, 2016 and updated on November 17, 2016.
November 17, 2016